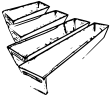
What Type of Drywall to Use
There are several types of drywall available on the market. The main types of drywall can be categorized as Standard, Lightweight, Fire Resistant, Moisture/Mold Resistant, and Abuse Resistant. Each of these main categories is also available in combinations of types. Here is a brief description of each of these main categories:
Standard Drywall
Standard drywall is the most widely recognized type of drywall on the market. It is used for most residential construction on walls and ceilings where a minimal fire rating is specified. Standard drywall is readily available in thicknesses of quarter-inch, three-eighths, and half-inch. When no specific type of drywall is required, Standard drywall is the best option since it is the easiest to work with and the least expensive. You can read more about the various thickness of drywall here.
Lightweight Drywall
Lightweight drywall first appeared on the mass market in the US in the early 2000s. When first introduced to the market it was sold basically as Standard drywall but made in a way that reduced the overall weight by up to 15%. It was first available in only half-inch thickness but soon thereafter was produced in other thicknesses as well.
Now, several different types of Lightweight drywall are available including Fire Rated, Mold Resistant, and even Fire Resistant Mold Resistant Lightweight Drywall. Where possible, Lightweight drywall is a great alternative since it is easier to work with than its Standard counterpart.
Fire Resistant Drywall
Fire Resistant Drywall can be broken down into three categories based on how well it holds up when subjected to intense fire. These categories are Standard Drywall, Firecode X, and Firecode C. In laboratory tests, Standard Drywall can withstand a fire of temperatures above 1800°F for about 10 minutes. Firecode X does better, lasting about 45 minutes. Firecode C provides the most fire resistance, lasting over an hour in similar tests.
Specific municipal regulations usually outline what level of fire rating is necessary for certain applications. Architectural drawings generally give details as to which type of drywall is required. As a general rule, Firecode X rated drywall is required when designing one-hour firewalls and Firecode C rated drywall is used in the design of up to three-hour firewalls. However, local building codes should be used to develop a specific building plan.
Moisture or Mold Resistant Drywall
Preventing water damage and mold growth is an important factor in the design of interior walls. Mold-resistant drywall panels are available in many different varieties. Mold grows in and on the paper used for drywall panels, not in the gypsum itself. Therefore, in order to prevent mold growth, manufacturing techniques address the paper that covers the front and back of the panels.
One type of drywall panel that claims resistance to mold has a surface paper on the front and back of the gypsum just like regular drywall. However, the paper used is embedded with a broad-spectrum antimicrobial additive said to resist mold growth. This type of Mold Resistant drywall can be installed and finished just like standard drywall. While it provides some protection against mold, it can fail when subjected to excessive or repeated moisture.
The second type of drywall that claims resistance to mold, eliminates the use of paper on the front and back of the gypsum. The surface of this type of drywall features a fiberglass mat front and back. This type of drywall usually also includes a broad-spectrum antimicrobial additive that prevents the growth of mold.
Because Fiberglass-mat drywall does not have a paper surface, extra work may be needed in finishing. Drywall seams can be taped and coated just like is done with standard drywall. If the finish called for exposes all or part of the drywall panel surface, a skim coat is needed before priming and painting. For example, as with all smooth wall finishes, one or perhaps two skim coat is needed with this type of drywall. Even with textures like, Knockdown, Skip Trowel, or Santa Fe, where some of the drywall panel shows through the texture, a skim coat is needed before painting.
Abuse Resistant Drywall
Abuse Resistant Drywall is designed to minimize two primary types of damage, surface damage and impact damage. Surface damage includes abrasion and indentation. Impact damage includes holes or cracks caused by impacts from soft bodies (humans, animals, bags) or hard bodies (tools, doorknobs, vacuum cleaners, baseballs, etc).
ASTM C1629 standards outline three levels of classification, Level 1 being the least resistant and Level 3 being the most resistant. Separate ASTM standards outline the testing methods needed to determine how well a gypsum panel performs before submitting being damaged. In testing for indentation or impact, different objects and methods are used but basically, the testing methods involve dropping or swinging a weighted object against a gypsum panel and measuring how much force it takes to dent or break through the drywall. For abrasion testing, a weighted wire brush is repeatedly scrubbed against the surface, and the depth of abrasion is measured.
When buying abuse-resistant drywall, look for the ASTM classification level. You may need to read the product information sheets to find the exact classification level.
Level 3 Abuse Resistant drywall is a good choice for industrial construction applications where incidental or intentional damage is expected. Level 1 or 2 may be suitable for residential use in areas like hallways where incidental damage is expected.
Sound Dampening Drywall
Sound-dampening drywall often is made with a layer of material in between two layers of gypsum. The layer in between dissipates or absorbs noise to prevent it from traveling to the other side. To achieve effective sound dampening, a complete system needs to be designed to eliminate noise. Sound dampening drywall is helpful but may not be enough depending on other factors such as framing, flooring, HVAC, plumbing, etc.
Exterior Drywall
There are two types of panels that are marketed as exterior drywall. The most common is exterior sheathing panels and the other is exterior soffit panels. Exterior sheathing panels are made to cover the exterior of a building as a base layer for siding. Though they are often listed along with other types of drywall, they have very little in common with drywall. They are usually made of gypsum and fiberglass, however, the intended use is as a replacement for plywood sheathing. In many ways, referring to these types of panels as drywall is more confusing than helpful.
The other type of exterior drywall is sometimes referred to as soffit board. It is made with a water-resistant gypsum core and water-repellent paper on the front and back. It is most often used on exterior porch ceilings just like standard drywall is used on interior ceilings. It can be taped, finished and textured like traditional drywall. Though this type of drywall is resistant to moisture, it will fail when exposed to extreme moisture. For this reason, it is most common in the Southwest US where the climate is dry.
Conclusion
Either standard drywall or fire-resistant type X drywall is most often the drywall of choice for construction. The other types of drywall are often used in certain situations on a worksite to supplement the main type used.